Exploring Prototype Injection Molds: A Game Changer for Metal Fabricators
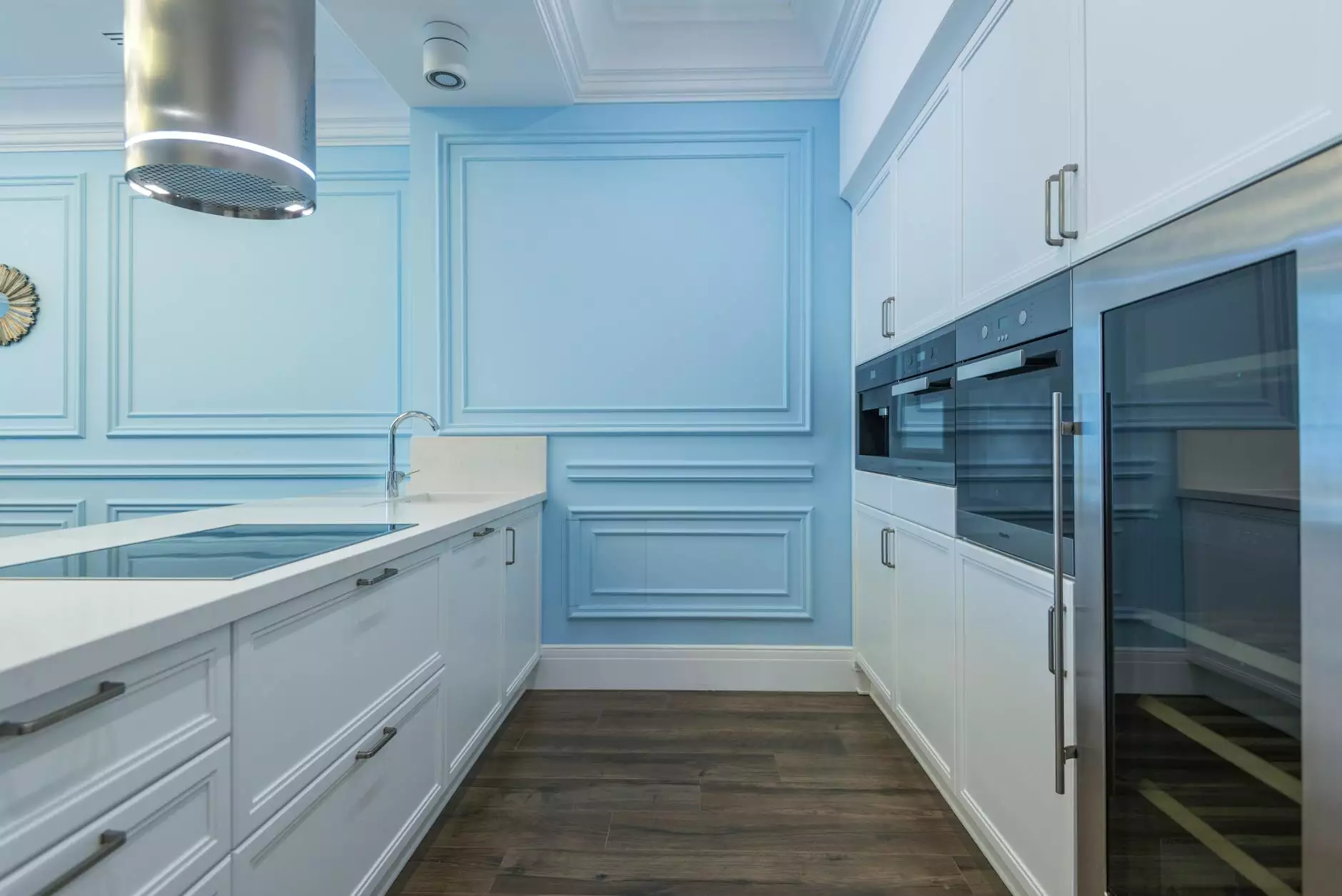
Prototype injection molds are at the forefront of manufacturing processes, significantly impacting how products are designed and created. As the manufacturing industry evolves, understanding the intricacies of these molds becomes paramount—especially for metal fabricators. This article delves into the world of prototype injection molds, illustrating their importance and benefits in the realm of metal fabrication.
What Are Prototype Injection Molds?
At their core, prototype injection molds are tools used to produce parts by injecting molten material into a mold cavity. They are specifically designed to create prototypes that are essential for testing and validating designs before mass production. This process enables fabricators to effectively produce intricate parts with high precision and repeatability.
The Anatomy of Prototype Injection Molds
Understanding the components that comprise a prototype injection mold is crucial for any metal fabricator aiming to enhance their processes:
- Mold Base: The foundation of the mold, providing stability and structure.
- Core and Cavity: The core forms the interior of the part, while the cavity shapes the outside.
- Cooling Channels: Designed to manage the temperature of the mold and ensure efficient production.
- Injection System: Mechanism for introducing the molten material into the mold.
- Ejector System: Used for removing the finished part from the mold.
The Importance of Prototype Injection Molds in Metal Fabrication
Prototype injection molds play an instrumental role in the metal fabrication sector. Here’s how:
1. Accelerated Product Development
In today’s fast-paced market, speed is essential. Prototype injection molds allow manufacturers to rapidly produce test parts that hasten the developmental phase of products. This agile approach helps to bring products to market faster than traditional methods, making it an essential tool for competitive advantage.
2. Cost-Effectiveness
Incorporating prototype injection molds can significantly reduce costs in the long run. By allowing metal fabricators to catch design flaws early in the product lifecycle, costly adjustments and delays during mass production can be avoided. This proactive approach to design leads to better resource allocation and enhanced profitability.
3. Enhanced Design Flexibility
The use of prototype injection molds offers immense flexibility in design. Metal fabricators can experiment with different materials and complex geometries without committing to full-scale production. This flexibility fosters innovation and can lead to superior product designs tailored to meet specific customer needs.
4. High Precision and Quality Assurance
Precision is a hallmark of successful metal fabrication. With prototype injection molds, manufacturers can achieve tight tolerances and consistent quality throughout the production process. This capability is crucial for industries demanding high levels of accuracy, such as aerospace and medical devices.
Types of Prototype Injection Molds
Metal fabricators have access to various types of prototype injection molds, each tailored to different requirements:
- Aluminum Molds: Lightweight and cost-effective, ideal for quick iterations.
- Steel Molds: More durable and suitable for repeated use, but at a higher cost.
- 3D Printed Molds: Allowing for rapid prototyping without the need for traditional machining.
The Process of Creating Prototype Injection Molds
The journey of developing a prototype injection mold involves several critical steps:
1. Design and Engineering
The first step is to design the part that the mold will create. Using CAD software, engineers can draft accurate designs that meet product specifications.
2. Mold Fabrication
Once the design is approved, the next step is to fabricate the mold. This can be done using traditional machining methods or advanced techniques such as 3D printing, depending on the type of mold required.
3. Testing and Validation
After fabrication, test runs are conducted to assess the mold's performance. This step is critical to ensure that the final product meets design specifications and quality standards.
4. Iteration
Based on the test results, adjustments may be necessary. This iterative process allows for refinements to be made before moving on to mass production.
Best Practices for Using Prototype Injection Molds
To maximize the benefits of prototype injection molds, here are some best practices that metal fabricators should follow:
1. Collaborate with Skilled Engineers
Working closely with experienced engineers can ensure that the mold design is optimized for performance. Their insights can lead to improved designs and reduced lead times.
2. Utilize Advanced Materials
The choice of materials for both the mold and the final product can greatly affect success. Consider using advanced polymers or composites that can withstand high pressure and temperature.
3. Embrace Technology
In today's digital age, leveraging technologies like CAD/CAM and simulation software can enhance design accuracy and facilitate faster prototyping processes.
4. Keep Iterative Testing a Priority
Regular testing during the prototyping phase helps identify issues early on, leading to improved final products and quicker time-to-market.
Future Trends in Prototype Injection Molds
The landscape of manufacturing is continuously evolving. Here are some emerging trends that are shaping the future of prototype injection molds:
1. Automation and Smart Manufacturing
As manufacturing processes become increasingly automated, the integration of smart technologies is set to enhance the efficiency and effectiveness of prototype injection molds.
2. Sustainable Practices
There is a growing emphasis on sustainability within the manufacturing sector. Prototype injection molding is likely to evolve to incorporate environmentally friendly materials and processes that minimize waste.
3. 3D Printing Advancements
Advancements in 3D printing technologies are expected to revolutionize mold making further, allowing for unique designs that were previously impossible to achieve with traditional methods.
Conclusion
In conclusion, prototype injection molds are essential tools for metal fabricators looking to enhance their manufacturing processes. They provide numerous benefits, including accelerated product development, cost-effectiveness, design flexibility, and high-precision manufacturing. By embracing best practices and staying abreast of industry trends, fabricators can leverage these molds to create innovative products that meet the evolving demands of today’s market.
For more insights and expert services in metal fabrication and prototype injection molds, visit deepmould.net.