The Importance of Precision Plastic Mold in Modern Manufacturing
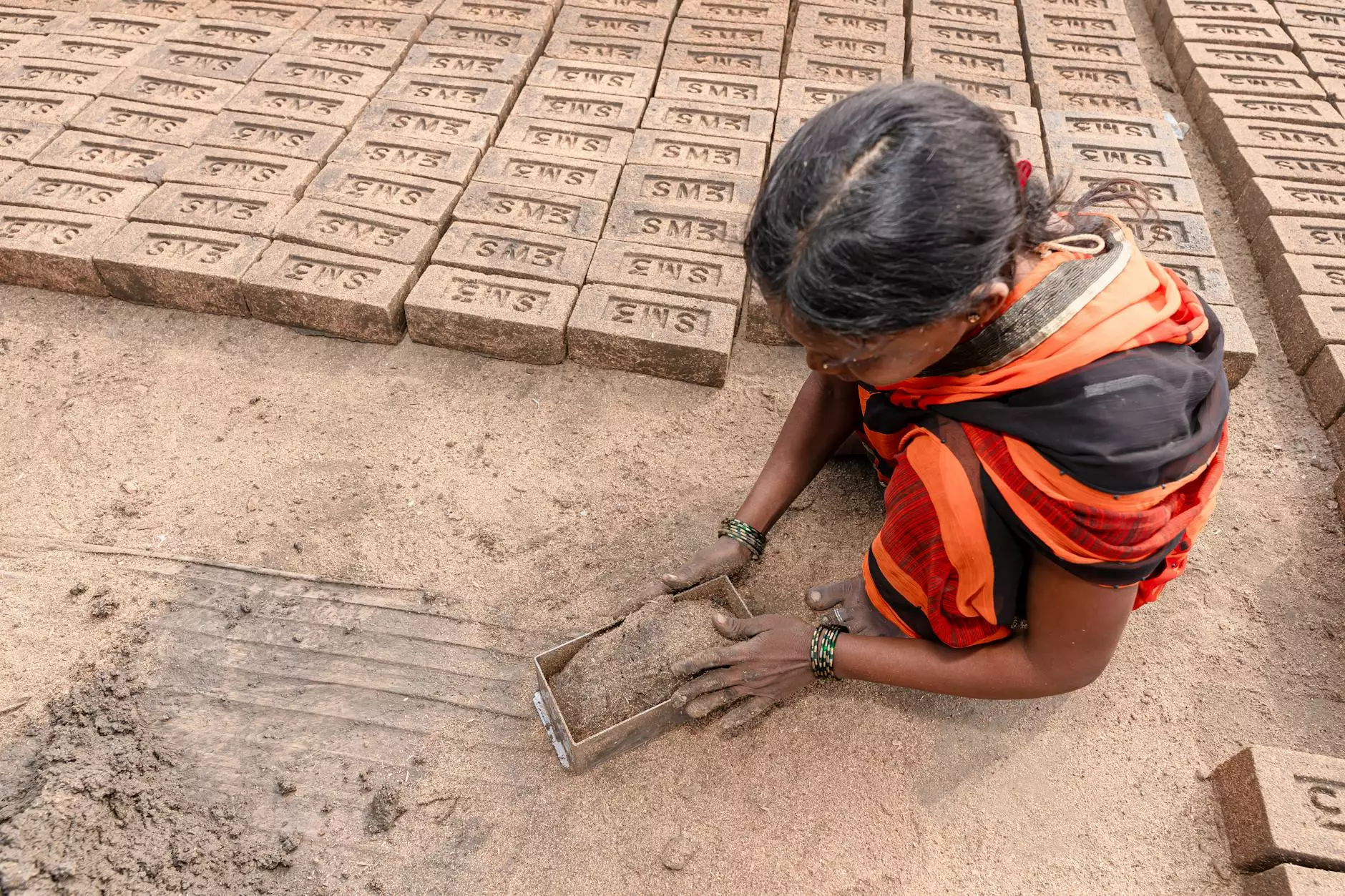
In today's rapidly evolving manufacturing landscape, the demand for precision and efficiency has never been greater. One of the most significant advancements that have shaped this industry is the use of precision plastic mold. This innovative technique not only enhances product quality but also maximizes productivity. In this article, we will delve deep into the world of precision plastic mold, exploring its benefits, applications, and the critical role of companies like DeepMould in shaping this sector.
What is Precision Plastic Mold?
Precision plastic mold refers to the specialized process of creating molds that produce plastic products with exact dimensions and superior quality. This technique employs advanced technology and meticulous engineering to ensure that every mold produced meets stringent specifications, which is crucial in industries where precision is paramount.
Key Advantages of Using Precision Plastic Mold
The benefits of incorporating precision plastic mold into manufacturing processes are numerous. Here are some of the most crucial advantages:
- Exceptional Accuracy: At the heart of precision molds is the unparalleled accuracy they offer. This is essential for industries where tolerances are tight and minor imperfections can lead to significant failures.
- Enhanced Material Efficiency: Precision molds are designed to minimize waste. By ensuring that materials are used effectively, manufacturers can reduce costs and environmental impact.
- Improved Surface Finish: Products produced using precision molds often exhibit superior surface finishes, leading to fewer post-processing requirements and higher overall quality.
- Rapid Production Rates: With precise molds, manufacturers can increase their output without compromising quality, which is vital in meeting market demands efficiently.
- Versatility: Precision plastic molds can be tailored for a wide range of applications, making them suitable for various industries, from automotive to consumer goods.
Applications of Precision Plastic Mold
Precision plastic molds are utilized across numerous sectors, showcasing their versatility and adaptability. Some of the primary applications include:
1. Automotive Industry
The automotive sector heavily relies on precision plastic molds for manufacturing interior and exterior components like dashboards, panels, and lighting systems. These components must meet rigorous safety standards and aesthetic considerations, making precision molding essential.
2. Medical Devices
In healthcare, the need for precision plastic molds is critical. Devices such as syringes, surgical tools, and implants require molds that not only deliver accuracy but are also made from biocompatible materials, ensuring safety for patients.
3. Consumer Electronics
From smartphone casings to intricate components within electronic devices, precision molds are integral in producing high-quality parts that fit together perfectly, enhancing the user experience.
4. Packaging Industry
Packaging solutions, particularly in food and pharmaceuticals, benefit greatly from precision molding. It ensures that containers, closures, and other packaging components are produced with the desired functionality and reliability.
Understanding the Manufacturing Process of Precision Plastic Mold
The creation of precise plastic molds involves several stages, each essential to ensuring a high-quality end product. Here is a detailed breakdown of the manufacturing process:
1. Design and Engineering
The process begins with detailed design and engineering work, where engineers use computer-aided design (CAD) software to create a 3D model of the mold. This stage involves evaluating various factors such as material selection, expected production volume, and tolerances.
2. Mold Fabrication
Once the design is finalized, the fabrication of the mold begins. Precision CNC machining is often utilized in this stage to ensure that the mold is crafted with exact specifications. This phase is crucial, as any inconsistencies can affect the final product's quality.
3. Surface Treatment
To enhance the performance of the molds, surface treatments may be applied. These treatments can improve durability, reduce friction, and enhance overall mold life.
4. Testing and Quality Control
Before manufacturing begins, the molds undergo rigorous testing. Quality control measures ensure that the molds can produce parts adhering to predefined standards, minimizing the risk of defects.
5. Production
After testing, production can commence. The mold is filled with plastic material, which is heated and injected into the mold cavity. After cooling, the mold is opened, and the finished part is ejected. This stage emphasizes the importance of precision, as any errors can lead to waste and increased costs.
The Role of DeepMould in Precision Plastic Mold Manufacturing
DeepMould has established itself as a leader in the precision plastic mold manufacturing industry. With years of experience and a commitment to quality, they have become a trusted partner for numerous businesses across various sectors. Here’s how DeepMould excels in this field:
1. Expertise and Experience
DeepMould's team comprises highly skilled professionals with extensive knowledge of injection molding technology. Their expertise ensures that clients receive personalized solutions tailored to their specific needs.
2. Cutting-Edge Technology
Utilizing the latest advancements in molding technology, DeepMould is capable of producing molds that meet the most stringent standards. This commitment to modernization enhances their manufacturing processes, ensuring efficiency and precision.
3. Custom Solutions
Understanding that every client has unique requirements, DeepMould offers custom solutions that cater to diverse applications. From concept to production, they guide clients through every step of the process, ensuring satisfaction.
4. Quality Assurance
Quality is a cornerstone of DeepMould's operations. Each mold undergoes comprehensive quality checks to ensure it meets high industry standards, which is vital in maintaining customer trust and satisfaction.
The Future of Precision Plastic Mold
The future of precision plastic mold manufacturing looks promising, with ongoing advancements in technology and processes paving the way for even greater efficiency and accuracy. Trends to watch include:
1. Automation and Smart Manufacturing
With the rise of automation in manufacturing, precision molds will benefit from智能制造 systems that leverage AI and machine learning. These technologies facilitate real-time monitoring and adjustments, enhancing production efficiency.
2. Sustainable Practices
As environmental consciousness grows, the demand for sustainable practices within precision molding will increase. Manufacturers will focus on using recyclable materials and processes that minimize waste, aligning with global sustainability goals.
3. Advanced Materials
The development of new materials, such as bio-based plastics, opens up opportunities for creating innovative products that meet both performance and environmental standards, further driving the evolution of precision plastic mold technology.
Conclusion
In conclusion, the significance of precision plastic mold in modern manufacturing cannot be overstated. With its numerous advantages and wide-ranging applications, it stands as a testament to the innovative spirit of the industry. Companies like DeepMould play a crucial role in advancing this technology, ensuring high-quality products that meet the ever-changing demands of the market. As we move forward, the continued evolution of precision molds will undoubtedly contribute to more efficient, sustainable, and high-quality manufacturing practices across the globe.
For more information about how DeepMould can help you with your precision molding needs, visit deepmould.net.