Injection Mold Plastics: A Game Changer in Metal Fabrication
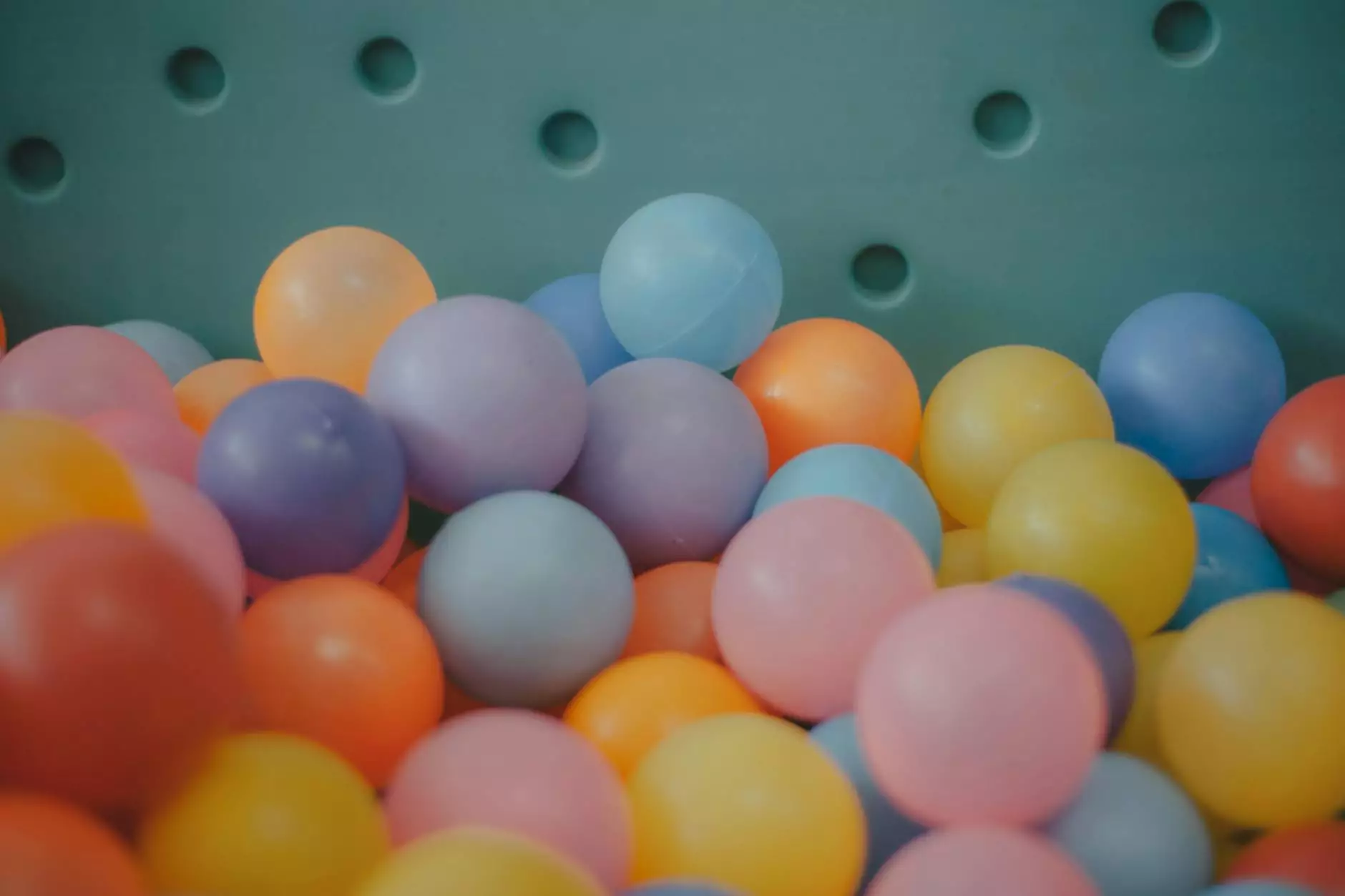
In today's industrial landscape, injection mold plastics have emerged as a pivotal element in the field of metal fabrication. As businesses seek to innovate and improve efficiencies, the integration of advanced materials and methods becomes essential. This article delves deep into how injection mold plastics are reshaping the industry, particularly for metal fabricators, providing unparalleled advantages that drive productivity and product quality.
The Basics of Injection Mold Plastics
Injection molding is a manufacturing process used to produce parts by injecting molten material into a mold. This technique primarily utilizes various types of plastics, including thermoplastics and thermosetting plastics. The flexibility and adaptability of injection mold plastics make them suitable for a wide range of applications in metal fabrication.
What are Injection Mold Plastics?
Injection mold plastics refer to the specific types of plastic used during the injection molding process. These plastics can be customized in terms of texture, flexibility, and color, catering to the diverse needs of different industries. Common types of injection mold plastics include:
- Polyethylene (PE)
- Polypropylene (PP)
- Polystyrene (PS)
- Polyvinyl Chloride (PVC)
- Acrylonitrile Butadiene Styrene (ABS)
- Polycarbonate (PC)
How Injection Molding Works
The injection molding process consists of several key stages:
- Material Preparation: Raw plastic pellets are prepared and dried to ensure optimal flow during molding.
- Melting: The plastics are heated to their melting point in a barrel.
- Injection: The molten plastic is injected into a mold at high pressure.
- Cooling: The material cools and solidifies within the mold.
- Demolding: The finished part is ejected from the mold.
The Significance of Injection Mold Plastics for Metal Fabricators
As industries evolve, the demand for high-quality, durable, and cost-effective solutions increases. Below are some significant advantages of using injection mold plastics in metal fabrication:
1. Cost Efficiency
Injection mold plastics can significantly reduce manufacturing costs. The ability to produce large volumes of parts with minimal waste contributes to lower operational costs. Additionally, the longevity of the molds reduces the need for frequent replacements, further enhancing cost savings.
2. Design Flexibility
The versatility of injection mold plastics allows for intricate and complex designs that may be challenging or impossible to achieve with traditional metalworking techniques. This enhances creativity in design, enabling metal fabricators to produce unique products that stand out in the market.
3. Lightweight Solutions
The use of plastics can significantly reduce the weight of products compared to metal-only solutions. This attribute is particularly advantageous for industries such as automotive and aerospace, where weight reduction correlates directly with fuel efficiency and performance.
4. Enhanced Durability
Modern injection mold plastics offer remarkable durability and resistance to various environmental factors, including moisture, chemicals, and UV exposure. This property makes these plastics suitable for both indoor and outdoor applications, extending the product lifecycle and reducing maintenance costs.
5. Improved Production Speed
The injection molding process allows for faster production rates without compromising quality. Once the initial setup is complete, manufacturers can produce thousands of identical parts in a fraction of the time required for traditional fabrication methods.
Applications of Injection Mold Plastics in Metal Fabrication
Injection mold plastics find applications across various sectors due to their desirable attributes. Some noteworthy applications in metal fabrication include:
1. Automotive Components
Many automotive parts, such as dashboards, bumpers, and interior fittings, utilize injection mold plastics due to their lightweight and durable nature.
2. Household Appliances
From casing for electronic devices to components in complex machinery, injection mold plastics enhance both functionality and aesthetics in household appliances.
3. Medical Devices
The medical field relies on precision-engineered components made from injection mold plastics, ensuring safety and compliance with stringent regulations.
4. Consumer Electronics
Devices such as smartphones and tablets often incorporate injection molded plastic components for their lightweight, robust, and appealing designs.
5. Packaging Solutions
Packaging manufacturers increasingly turn to injection mold plastics to create durable, cost-effective, and environmentally friendly packaging options.
Best Practices for Working with Injection Mold Plastics
For metal fabricators, understanding the intricacies of working with injection mold plastics is crucial to achieving optimal results. Here are some best practices to consider:
1. Choose the Right Material
Selecting the appropriate type of plastic is essential. Consider factors such as strength, chemical resistance, thermal stability, and cost when choosing the right material for specific applications.
2. Optimize Mold Design
An effective mold design ensures proper flow of plastic material and minimizes defects. Collaborate with experienced mold designers to achieve precise mold specifications tailored to the intended application.
3. Monitor Temperature and Pressure
Maintaining the proper temperature and pressure throughout the injection molding process is vital for ensuring consistent quality. Regular monitoring can help identify potential issues before they affect production.
4. Conduct Regular Maintenance
Routine maintenance of molds and equipment is essential in preventing breakdowns and ensuring continuous operation. Establish a maintenance schedule to keep machinery in optimal condition.
5. Invest in Employee Training
Providing comprehensive training for personnel involved in the injection molding process enhances operational efficiency and safety. A skilled workforce is instrumental in producing high-quality products.
Future Trends in Injection Mold Plastics
The landscape of injection mold plastics continues to evolve, influenced by technological advancements and changing consumer demands. Some trends include:
1. Sustainable Plastics
With increasing environmental concerns, the demand for sustainable and biodegradable injection mold plastics is on the rise. The industry is shifting its focus towards developing eco-friendly materials that do not compromise performance.
2. Smart Plastics
The advent of smart materials embedded with sensors and data-collecting capabilities offers exciting possibilities for the future of injection mold plastics, particularly in high-tech applications.
3. 3D Printing Integration
Combining traditional injection molding with 3D printing processes can optimize production, allowing for the creation of complex geometries that improve function and efficiency.
Conclusion
Injection mold plastics represent a transformative force in the metal fabrication industry. Their unique properties, economic advantages, and diverse applications make them an indispensable resource for modern manufacturers. By adopting best practices and staying informed about trends, metal fabricators can harness the full potential of these materials, paving the way for innovative and cost-effective solutions in an increasingly competitive market.
Call to Action
If you're interested in integrating injection mold plastics into your manufacturing processes, contact deepmould.net today. Our experts are ready to help you optimize your operations and achieve your production goals.