The Significance of Die Cast Mold Manufacturers in Today's Metal Fabrication Industry
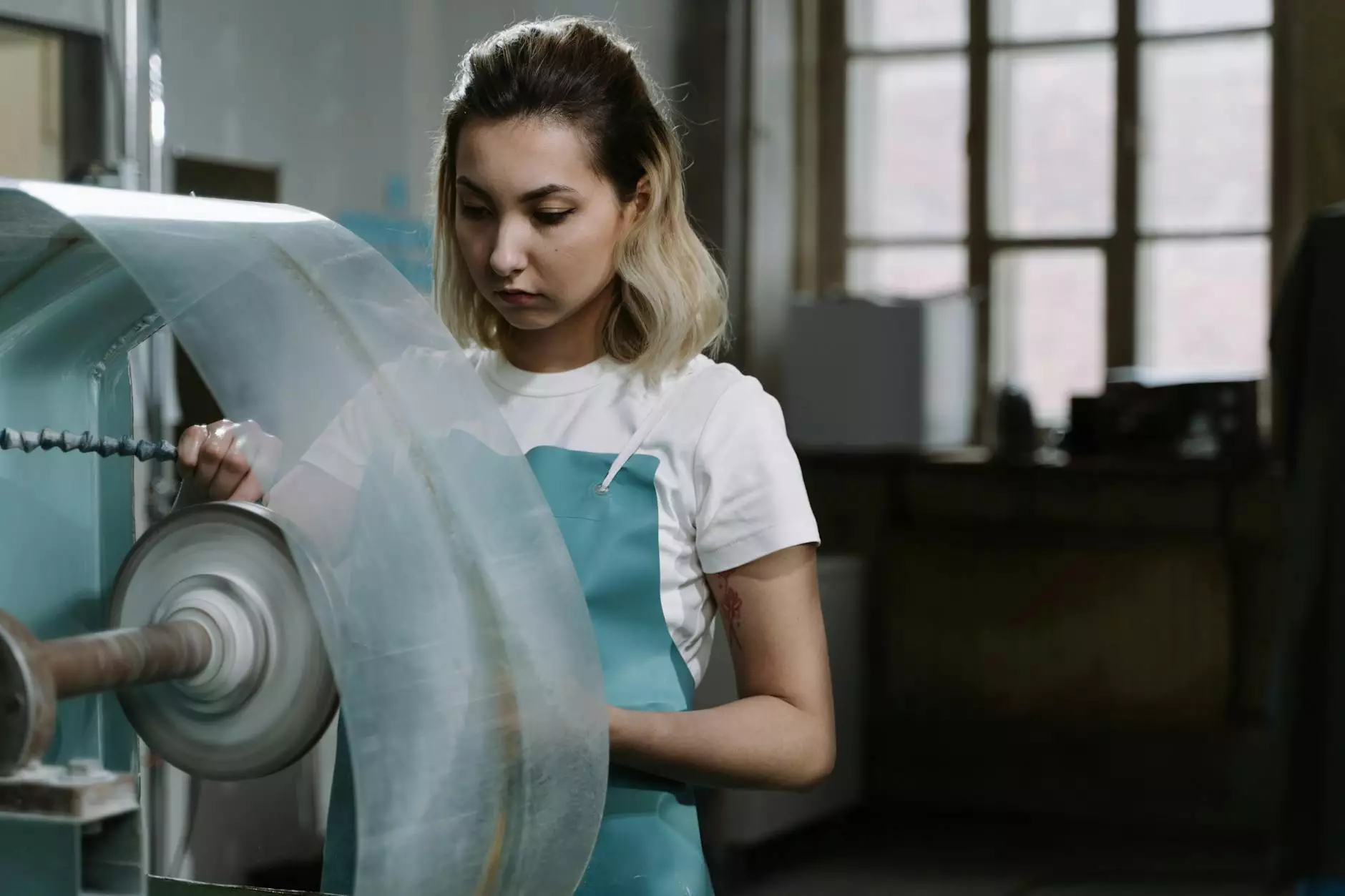
In the ever-evolving landscape of manufacturing, die cast mold manufacturers play a pivotal role in shaping the industry. As we delve into this dynamic sector, we uncover not only the technical intricacies involved in mold production but also the broader implications of these processes on various industries, including automotive, aerospace, and consumer electronics.
Understanding Die Casting: A Brief Overview
Die casting is a process that involves forcing molten metal into a mold cavity under high pressure. This production technique allows for precise dimensional control and excellent surface finish, making it a preferred method in various applications. The die cast mold manufacturers are responsible for creating the molds that define the shape and quality of the final products.
The Die Casting Process Explained
The die casting process can be broken down into several key stages:
- Preparation of Materials: High-quality metal, usually zinc, aluminum, or magnesium, is melted in a furnace.
- Mold Heating: The mold is pre-heated to facilitate better flow of molten metal and to ensure the strength of the die cast product.
- Injection of Molten Metal: Molten metal is injected into the mold under high pressure.
- Cooling and Solidification: The metal cools and solidifies in the mold, taking its shape.
- Mold Opening: After cooling, the mold is opened, and the finished component is ejected.
The Importance of Quality in Die Cast Mold Manufacturing
The quality of the die cast molds directly impacts the efficiency of the die casting process and the properties of the final products. Here are some key considerations:
Material Selection
Quality molds are typically made from durable materials such as:
- Tool Steel: Known for its hardness and wear resistance.
- Aluminum: Offers lightweight properties and easier machining.
- Alloy Steels: Provide a blend of hardness and toughness.
Precision Engineering
Die cast mold manufacturers leverage advanced technologies like CNC machining and CAD/CAM software to achieve unmatched precision and accuracy in mold creation. This level of accuracy minimizes defects and reduces post-casting operations.
Applications of Die Cast Mold Manufacturing
Die casting is employed across a multitude of industries, showcasing the versatility and significance of die cast mold manufacturers:
Automotive Industry
The automotive sector is one of the largest consumers of die cast components. Components such as engine blocks, transmission cases, and various structural parts use die casting due to its ability to produce lightweight and complex shapes, leading to fuel efficiency and performance enhancement.
Aerospace Applications
In aerospace, die cast molds are utilized for manufacturing components that require high precision and durability. From structural parts to critical components in aircraft engines, die casting plays a vital role in ensuring safety and reliability.
Consumer Electronics
Modern consumer electronics, including laptops, smartphones, and home appliances, heavily utilize die cast components. The lightweight and strong properties of die cast aluminum and zinc make them ideal for creating housings, frames, and decorative parts.
The Future of Die Cast Mold Manufacturing
As industries continue to evolve, so too do the technologies and processes employed by die cast mold manufacturers. Here are a few trends that are shaping the future:
Increased Automation
The integration of robotics and automated systems in the manufacturing process is enhancing efficiency and consistency. Advanced machinery can operate with minimal human intervention, reducing labor costs and increasing output rates.
3D Printing in Mold Design
3D printing technologies are revolutionizing mold design and prototyping. By allowing for rapid iterations and modifications, manufacturers can streamline the development process, reducing time-to-market and enhancing innovation.
Environmental Considerations
As sustainability becomes a larger concern, die cast mold manufacturers are exploring eco-friendly practices. This includes the recycling of materials and energy-efficient processes that minimize waste and reduce the carbon footprint.
Choosing the Right Die Cast Mold Manufacturer
When selecting a die cast mold manufacturer, it's essential to consider several factors to ensure quality and reliability:
Experience and Expertise
Select a manufacturer with years of experience and a proven track record in the industry. Their expertise can translate into higher-quality molds and finished products.
Technology and Machinery
Assess the technologies and machinery used by the manufacturer. State-of-the-art equipment often results in greater precision and efficiency, leading to superior quality molds.
Customer Support and Service
Robust customer support and post-manufacturing services can make a significant difference in your overall experience. Consider manufacturers that offer comprehensive services, including design assistance and maintenance.
Conclusion: The Vital Role of Die Cast Mold Manufacturers
In conclusion, die cast mold manufacturers stand at the forefront of the manufacturing industry, facilitating innovation, efficiency, and quality in numerous applications. By understanding the processes, importance, and future trends of die casting, businesses can make informed decisions that enhance their production capabilities and product quality. As we move forward, embracing technology and sustainable practices will be crucial for maintaining competitiveness in an increasingly demanding market.
For businesses seeking reliable die cast mold manufacturers, look no further than deepmould.net, where proficiency meets quality in the realm of metal fabrication.