Aaron Metosky Designs - Business and Consumer Services - Digital Marketing
Cool Manufacturing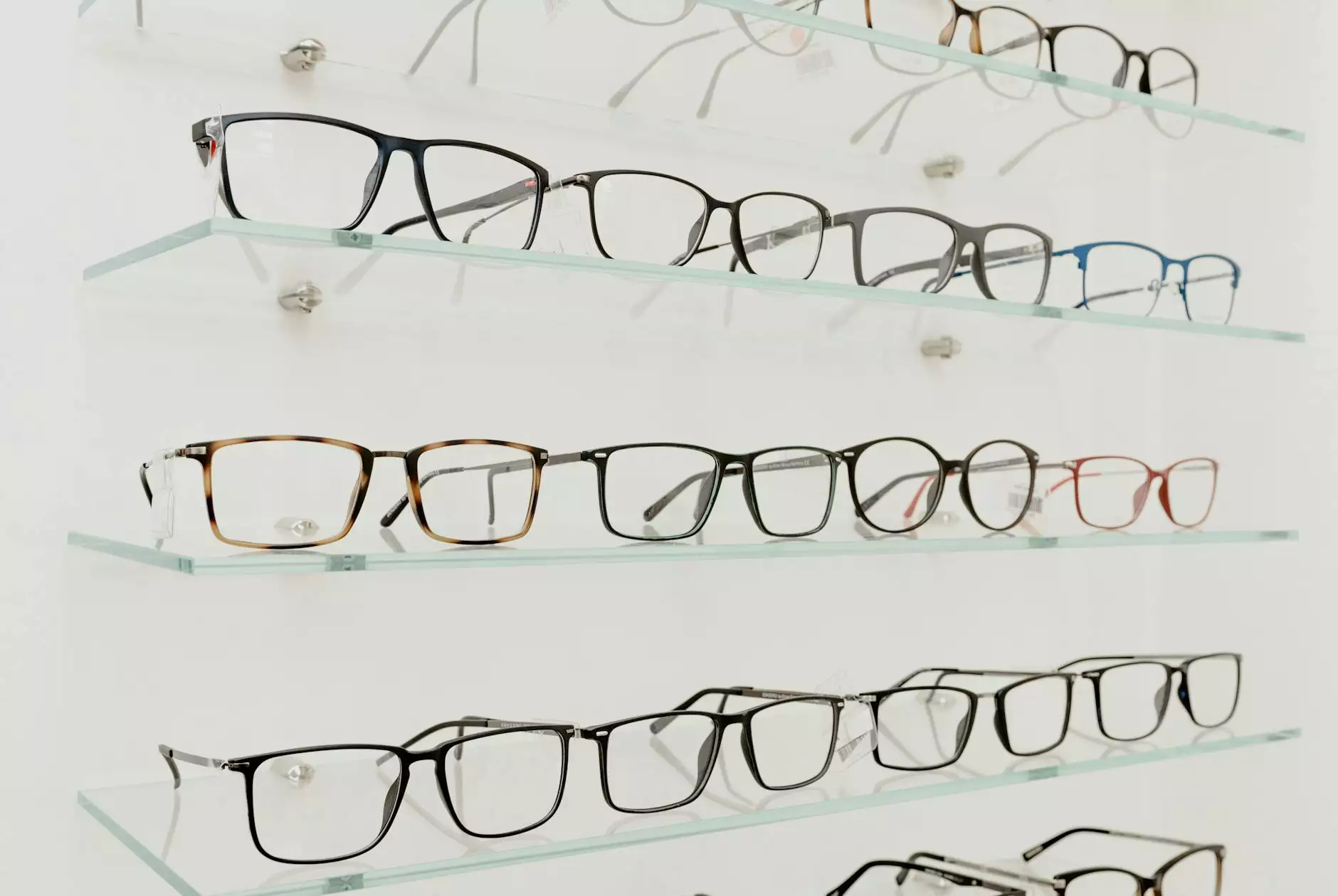
Root Cause Analysis (RCA) in Manufacturing - MANTEC
Welcome to the comprehensive guide on Root Cause Analysis (RCA) in manufacturing. In this article, we will explore what RCA is, its importance in the manufacturing industry, and how MANTEC provides exceptional RCA services tailored to the specific needs of businesses.
What is Root Cause Analysis (RCA)?
Root Cause Analysis, commonly known as RCA, is a systematic approach to problem-solving used to identify the underlying causes of issues or failures within a manufacturing process. It helps businesses understand the specific reasons behind problems and empowers them to implement effective solutions to prevent their recurrence.
The Importance of RCA in Manufacturing
In the fast-paced world of manufacturing, identifying and addressing the root causes of issues is essential for optimizing efficiency, productivity, and overall quality. By conducting thorough RCA, businesses can prevent costly failures, reduce downtime, eliminate waste, and ensure continuous improvement.
MANTEC: Your RCA Partner
As a leading provider of digital marketing services in the business and consumer services category, Aaron Metosky Designs proudly partners with MANTEC to offer top-notch RCA services to manufacturing businesses. With years of industry experience and a team of dedicated professionals, we are committed to helping businesses overcome challenges and achieve their operational goals.
Our Approach
At Aaron Metosky Designs, our approach to RCA is rooted in a deep understanding of manufacturing processes and industry best practices. We follow a proven methodology that involves:
- Problem Identification: We work closely with your team to identify the issue or failure that requires RCA.
- Data Collection: Our experts gather relevant data, analyze process documentation, and collect evidence to get a comprehensive view of the problem.
- Analysis: Using various analytical tools and techniques, we dissect the collected data to uncover the root causes of the issue.
- Solution Implementation: Based on the RCA findings, we develop practical and preventive solutions that address the root causes and minimize the risk of future occurrences.
- Monitoring and Evaluation: We track the effectiveness of the implemented solutions, continuously monitor performance, and make adjustments if necessary.
Benefits of our RCA Services
- Increased Efficiency: Our RCA services enable businesses to optimize their operations and identify areas for improvement, resulting in enhanced efficiency.
- Productivity Improvement: By addressing the root causes of issues, we help businesses streamline their processes, reducing downtime and increasing productivity.
- Quality Enhancement: With better understanding and control of the underlying causes, businesses experience improved product quality and customer satisfaction.
- Cost Reduction: RCA helps eliminate waste, prevent recurring issues, and minimize costly failures, leading to significant cost savings.
- Continuous Improvement: Through our RCA services, businesses can foster a culture of continuous improvement, driving long-term success and sustainability.
Contact Us for Effective RCA Services
If you're looking for the best RCA services in the manufacturing industry, Aaron Metosky Designs and MANTEC have you covered. Our team of experts is ready to assess your unique challenges and develop tailored solutions that address the root causes, helping you achieve operational excellence in your business. Contact us today to schedule a consultation and take the first step towards optimized efficiency, productivity, and quality.